Nachdem ich neulich über die Technik und die Software einer „analogen“ Uhr berichtet habe, geht es jetzt um den Bau der eigentlichen Uhr. Um eine hohe Präzision zu erreichen, habe ich die meisten Arbeitsschritte mit dem Lasercutter der warpzone durchgeführt. Hierzu musste ich mich auch in die Software Inkscape einarbeiten.
Planung der Uhr
Während ich im letzten Artikel noch einen LED-Ring von AliExpress benutzt habe, habe ich mich in der Zwischenzeit dazu entschieden, einen Meter WS2812B LED-Streifen mit 60 LEDs zu verwenden. Diese sollen seitlich auf etwas aufgeklebt werden und ihr Licht 360° von der Uhr weg an die Wand / Rückplatte werfen. Als Frontplatte dachte ich an etwas transparentes oder milchig transparentes, auf das direkt vorne drauf die Technik montiert werden sollte.
Wahl des Werkzeuges
Es sollte billig sein, gut aussehen und ich wollte es selbst machen. Also entschied ich mich frühzeitig für eine computergestützte Fertigung. Zur Wahl standen 3D-Drucker, C&C-Fräse oder Lasercutter.
Die C&C Fräse, auf die ich über einen Kumpel Zugriff habe, wird lokal am Gerät programmiert, daher ist sie recht frühzeitig ausgeschieden. Hier hätte ich das Werkstück nicht ohne Weiteres vorbereiten können. Natürlich hätte ich hier wieder die Hilfe des Kumpel beanspruchen können, aber ich wollte durchaus meinen Horizont erweitern.
Der 3D Drucker fiel wegen zu kleinem Arbeitsbereich raus. Und ich hätte Probleme wie den Überhang der Frontplatte entweder mit Stützstruktur oder mit Einzelteilfertigung lösen müssen. Außerdem werden durchscheinende Flächen auch nicht so homogen, wie ich mir die Uhr vorgestellt habe.
Aufgrund der einfachen Struktur, die ich im Kopf hatte, entschied ich mich letztendlich für den Lasercutter. Als Material habe ich im Baumarkt günstiges Sperrholz und Reststücke an transparentem und milchigem Plexiglas besorgt.
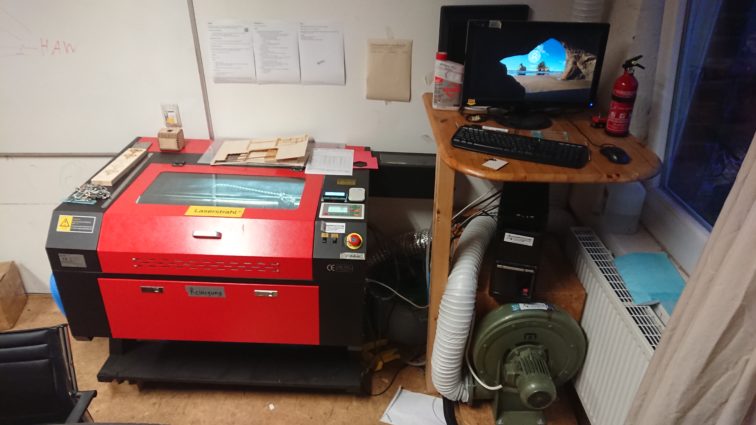
Wichtig bei der Materialwahl ist, dass beim Schneiden / Gravieren kein Chlor freigesetzt wird. Dies legt sich auf den Goldspiegeln nieder und zerstört effektiv das Gerät. Damit fallen alle PVC-Kunststoffe raus. Die Absaugung filtert zwar die Luft mit einem Aktivkohlefilter und Textilmesh, aber allzu giftig sollten die Verbrennungsprodukte auch nicht sein. Optimalerweise sollte das Material unter dem Laserstrahl verdampfen und nicht schmelzen. So werden die Schnittkanten schön sauber. Diese Anforderungen erfüllt das Plexiglas Material PMMA. Durch die PE Folie kann problemlos durchgeschnitten werden. So setzen sich keine Reste verdampften Materials am Werkstück ab.
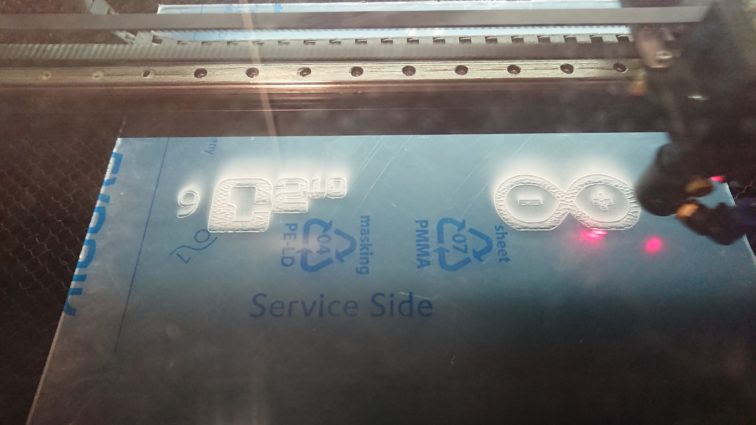
Wie sich später herausgestellt hat, bildet die PE-Folie allerdings beim Gravieren Tropfen und verschmilzt zu einer rauen Oberfläche.
Design der Schnittmuster und Gravur
Die Software des Lasers nimmt als Schnittvorlage Vektoren im .dxf-Format. Diese Pfade in verschiedenen Farben können einzeln aktiviert werden und jeder Farbe können Parameter wie Abfahrgeschwindigkeit und Laserintensität zugeordnet werden. Gravuren nimmt die Software lieber als Rasterbild, z. B. im .png-Format.
All das kann ich mit Inkscape problemlos erreichen, sowohl unterschiedlich farbene Vektoren für die Schnitte, als auch den Export des zu gravierenden Ziffernblattes im .png-Format.
Grundsätzlich dachte ich mir, dass ich einen Mittelkorpus aus Sperrholz brauche. Dahinter soll eine größere kreisrunde Platte sein, die als Reflektor dient, damit man die LEDs gut sehen kann. Die Frontplatte sollte ebenfalls 1cm Überhang haben, damit man nicht geblendet wird, wenn man direkt in die LEDs schaut.
Das .svg ist in 4 Ebenen aufgeteilt. Jedes Objekt ist hierarchisch korrekt platziert und beschriftet. Die Ebenen wie die Objekte können einzeln ein- und ausgeblendet werden. Ebenso ist ein etwaiger Export einzelner Ebenen problemlos möglich. Ferner ist noch eine unsichtbare Ebene mit den Abmessungen und Bohrlöchern für Arduino Uno und Arduino Mega vorhanden. Anhand dieser habe ich die Bohrlöcher für den Arduino platziert. Alles ist zusammen mit dem angepassten Code im Gitlab-Repository verfügbar und als Archiv am Ende des Artikels angehängt.
Mittelkorpus (Barrel, schwarz)
Die Streifen sind exakt 1cm breit, bei 4mm starkem Sperrholz brauche ich das Teil 3x um mit 12mm Dicke hinreichend viel Platz zu haben. Der Außenumfang soll exakt 1m betragen, so kann ich genau 60 LEDs darauf unterbringen. Allerdings muss hier im Innenraum Platz für die Verkabelung und den verborgenen Teil von Dreh-Potentiometer und Button sein.
Rückplatte (Backplate, blau)
Die Rückplatte ist das einfachste Teil, es hat nur ein Loch für die Kabeldurchführung.
Gravurlayer (Engraving, orange)
Der Layer „Engraving“ ist ein Sublayer von „Frontplate“ und sollte als erstes vor den Ausschnitten durchgeführt werden, da sich die Teile beim Herausschneiden bewegen könnten. Ich musste diesen Layer als .png exportieren für die verwendete Software.
Frontplatte (Frontplate, rot)
Dies ist das komplexeste Werkstück und wird in meinem Fall aus milchig transparentem Plexiglas herausgeschnitten. Hier sind die Ausschnitte für Button, Poti, die Schraublöcher für den Arduino und die Kabeldurchführungen eingezeichnet.
Anfertigen der Einzelteile
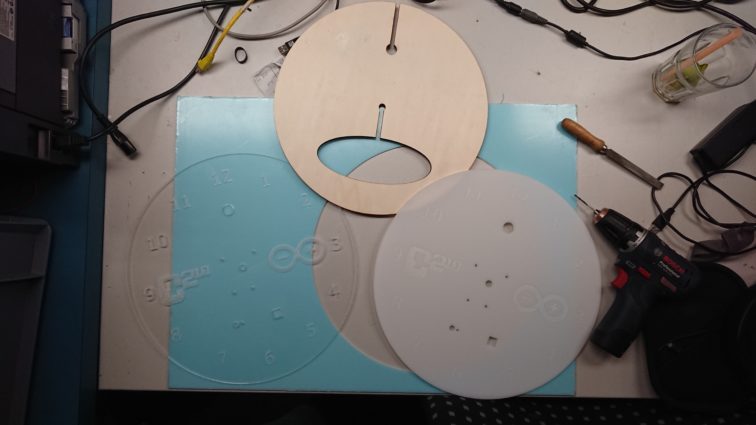
Zusammenfügen des Holzteils
Nun habe ich die Holzteile miteinander verleimt. Ich richte die Einzelteile anhand der Bohrlöcher übereinander aus. In der Rückplatte ist nur ein Loch, hier musste ich zusätzlich den Abstand des Mittelteils zum Rand mit dem Lineal ausmessen. Zusammen mit dem Kabelloch konnte ich auch diese zentrieren.
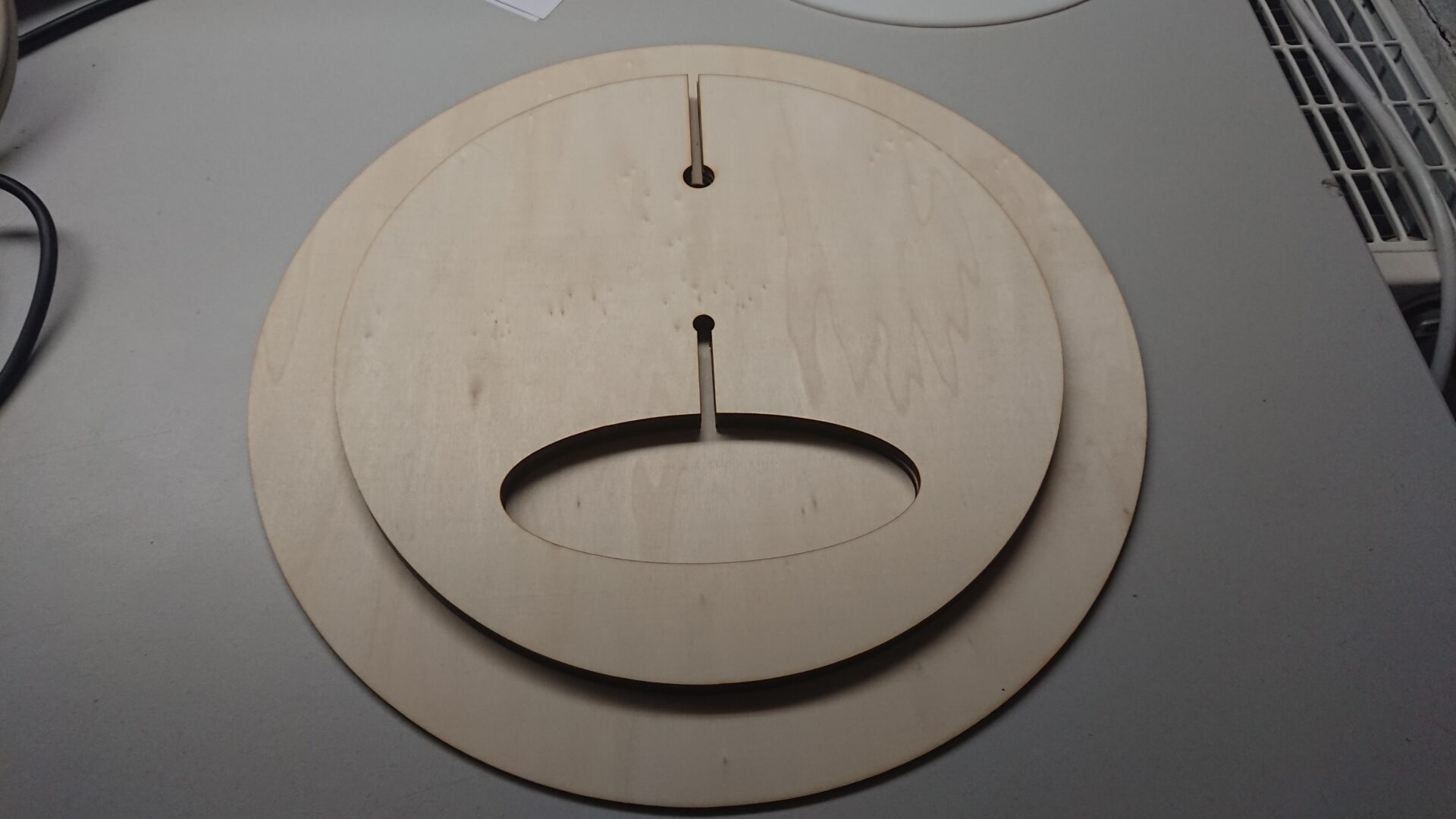
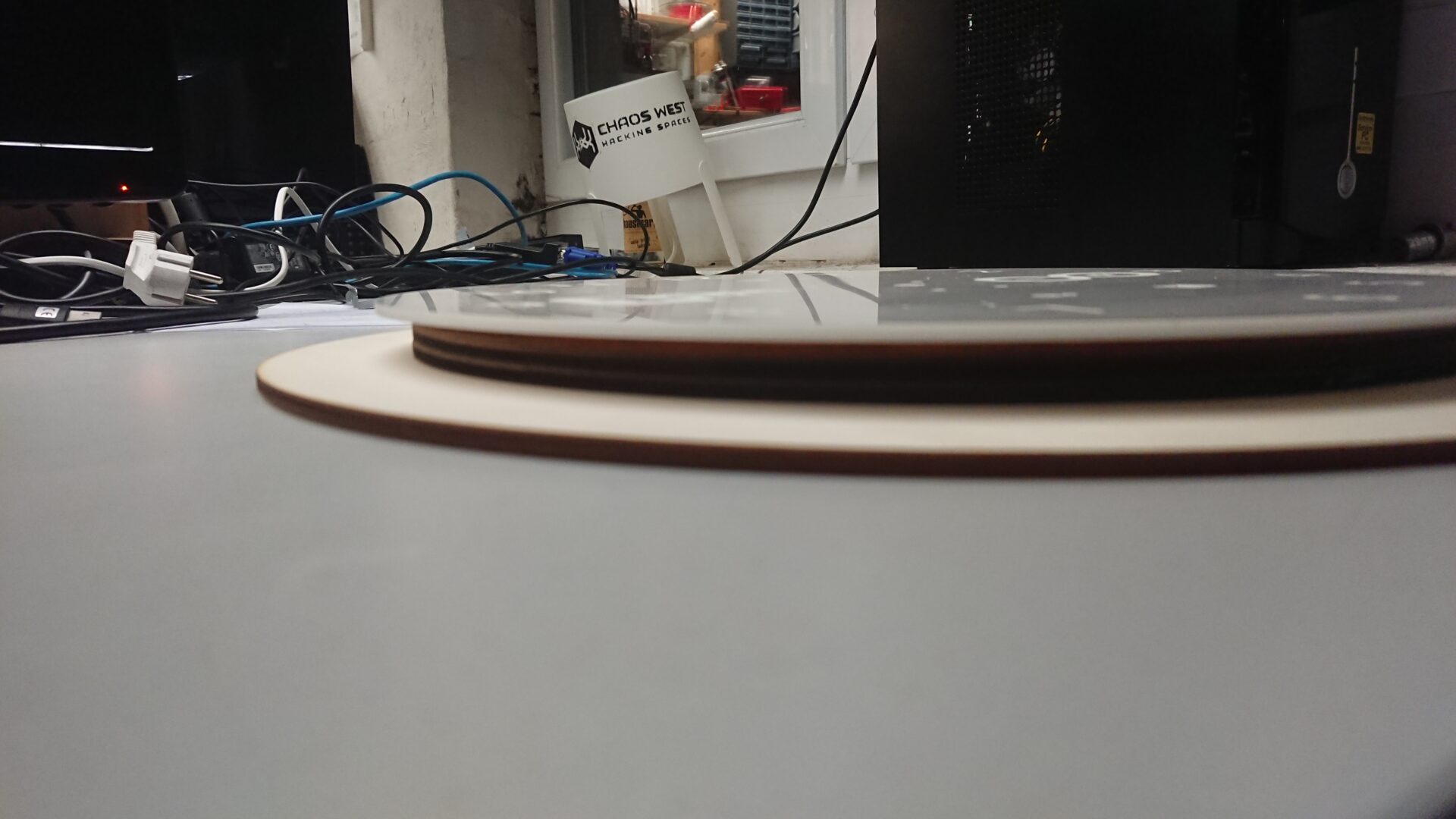
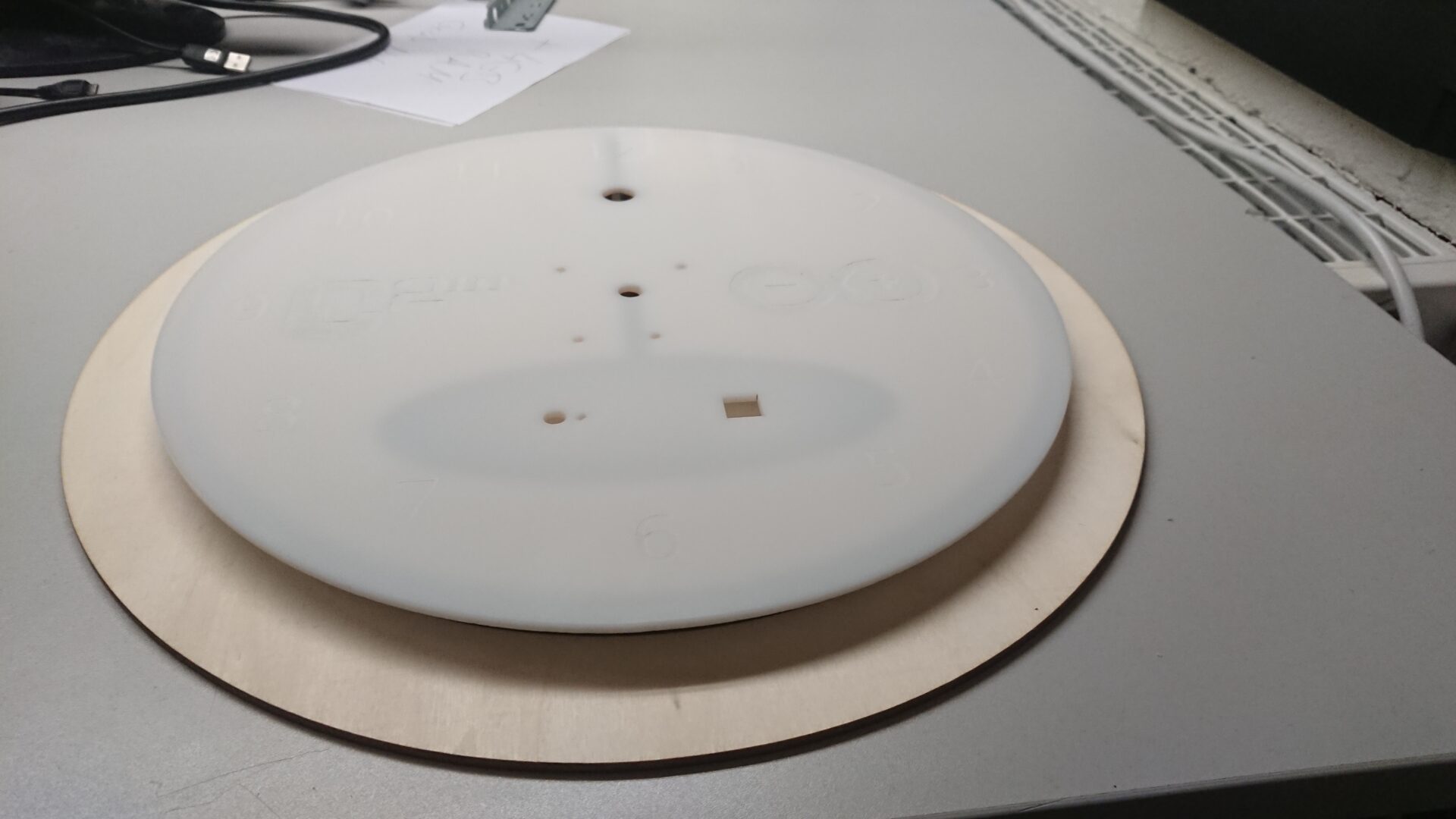
Die Frontplatte wird später verschraubt, um einen Zugang für Reparaturen oder Veränderungen zu gewährleisten. Eine weitergehende Verschraubung hatte ich bei meinem Prototypen nicht vorgesehen. Es ist jedoch ein Leichtes, das ganze Konstrukt komplett mit nem Metall- oder Holzbohrer zu durchbohren und mit 25mm Maschinenschrauben zu fixieren. Genauso gut könnte man entsprechende Löcher auf allen Layern (sprich in allen 3 Farben übereinander) hinzufügen.
Lackieren des Holzteils der Uhr
Dieser Schritt ist recht trivial. Eine Dose Kunststoffgrundierung und mattweißen Lack aus dem Baumarkt erfüllt den Job. Logischerweise grundiere ich zuerst. Nach einer Stunde des Antrocknens habe ich direkt den weißen Lack aufgetragen. Dies kann nun ein paar Stunden – oder besser über Nacht – trocknen. Je nach Deckkraft des Lacks muss dieser Schritt noch ein zweites mal wiederholt werden.
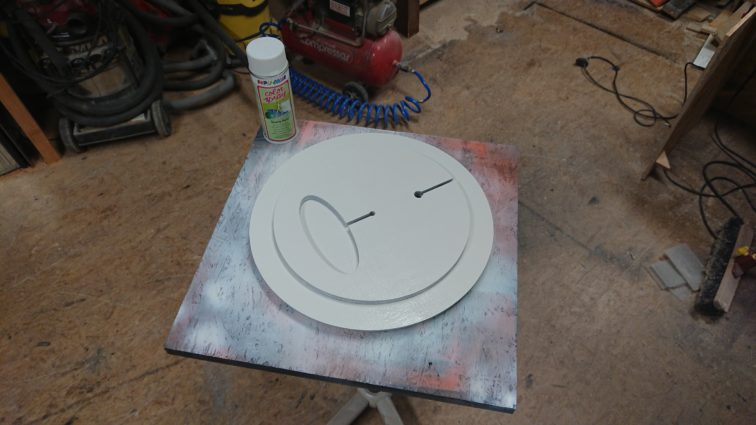
Endmontage der Uhr
Ich lötete nun Drahtstücke an die Kontakte von Button und Poti, die viel zu lang waren. Kürzen der Kabel kann dann später erfolgen. Den Button habe ich mit Pattex Express in die Aussparung geklebt, den Poti konnte ich mit der Nase an der Seite fixieren und mit der Mutter festschrauben. Die Kabel werden durch den Schlitz aus dem ovalen Ausschnitt durch das zentrale Loch nach oben herausgeführt.
Den Arduino befestige ich mit ca 3cm langen Holzschrauben durch die vorgesehenen Löcher hindurch am Holzkorpus, wobei ich 0.5cm Plastikabstandshalter zwischen Frontplatte und Technik platziert habe. So habe ich genug Luft unter dem Gerät, um die Kabel herauszuführen.
Netzwerkkabel und Strom werden durch das Loch im oberen Drittel hindurchgeführt – ebenso wie die 3 Leitungen für die LED-Streifen. Letztere verlaufen dann durch den Schlitz bis zum Rand des Mittelteils, um den im Uhrzeigersinn angebrachten LED-Streifen zu erreichen.
Stromversorgungs- und Netzwerkkabel habe ich bei mir im Wohnzimmer im hinter der Uhr verlaufenden Kabelkanal versteckt.
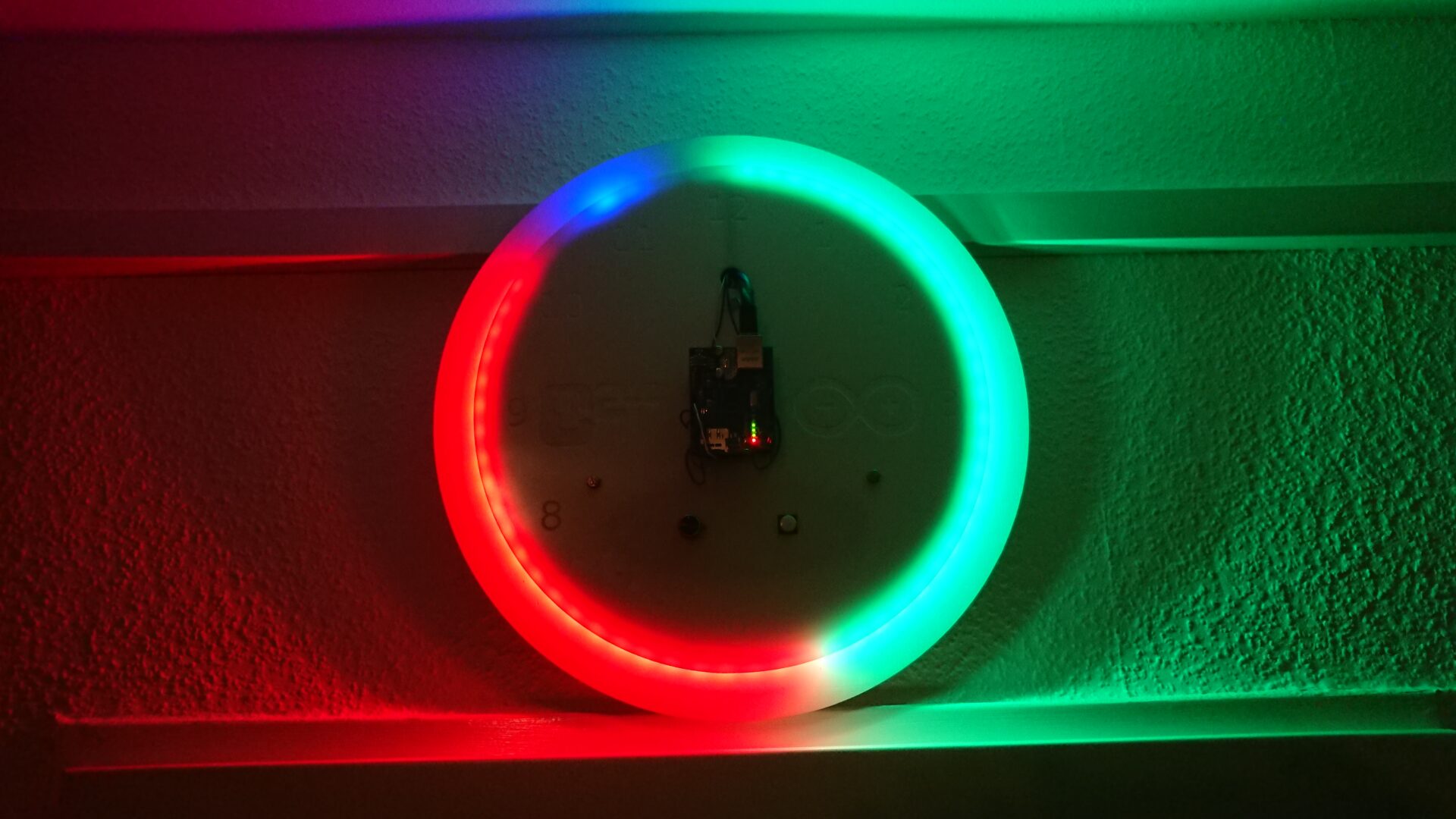
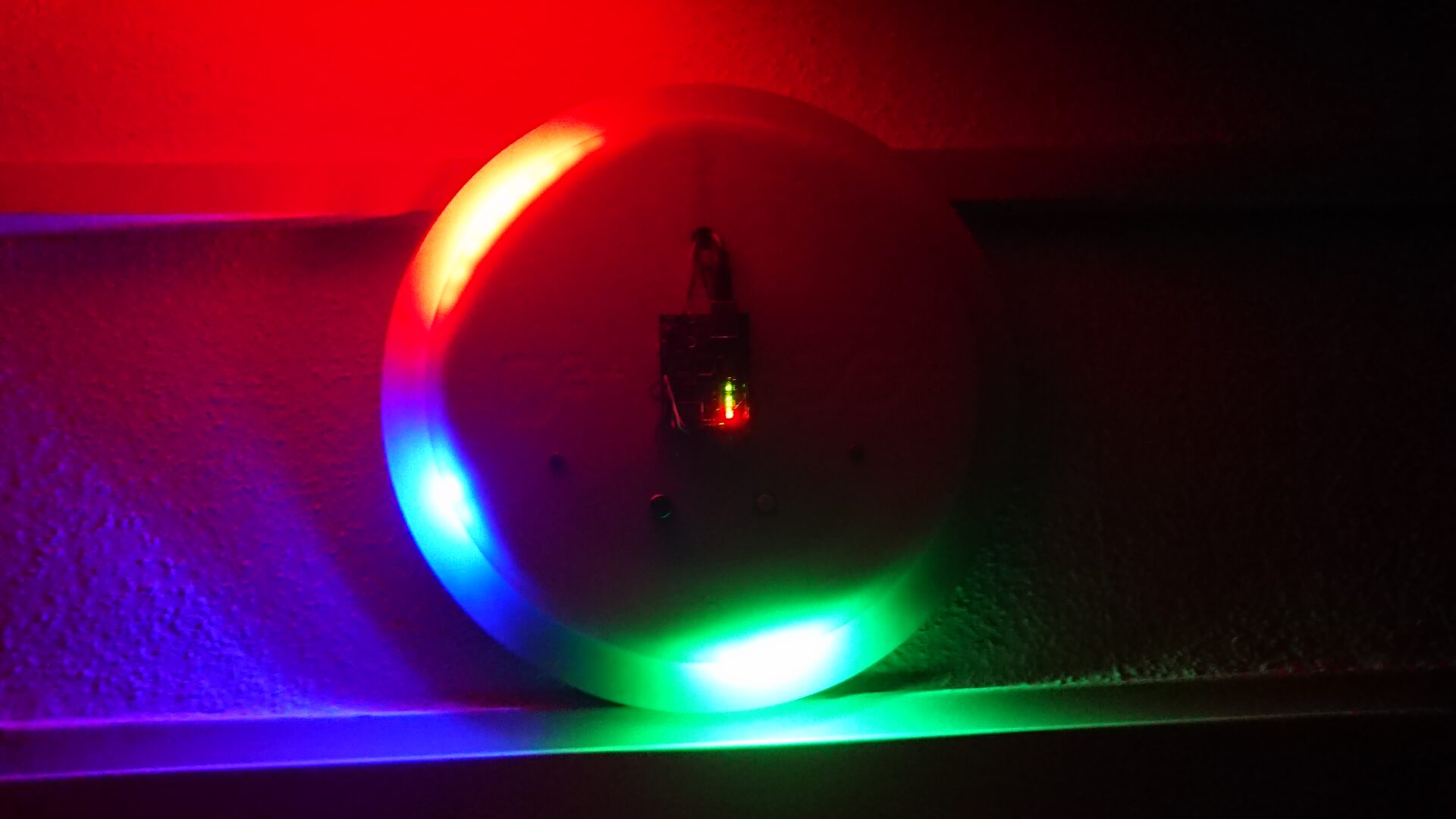
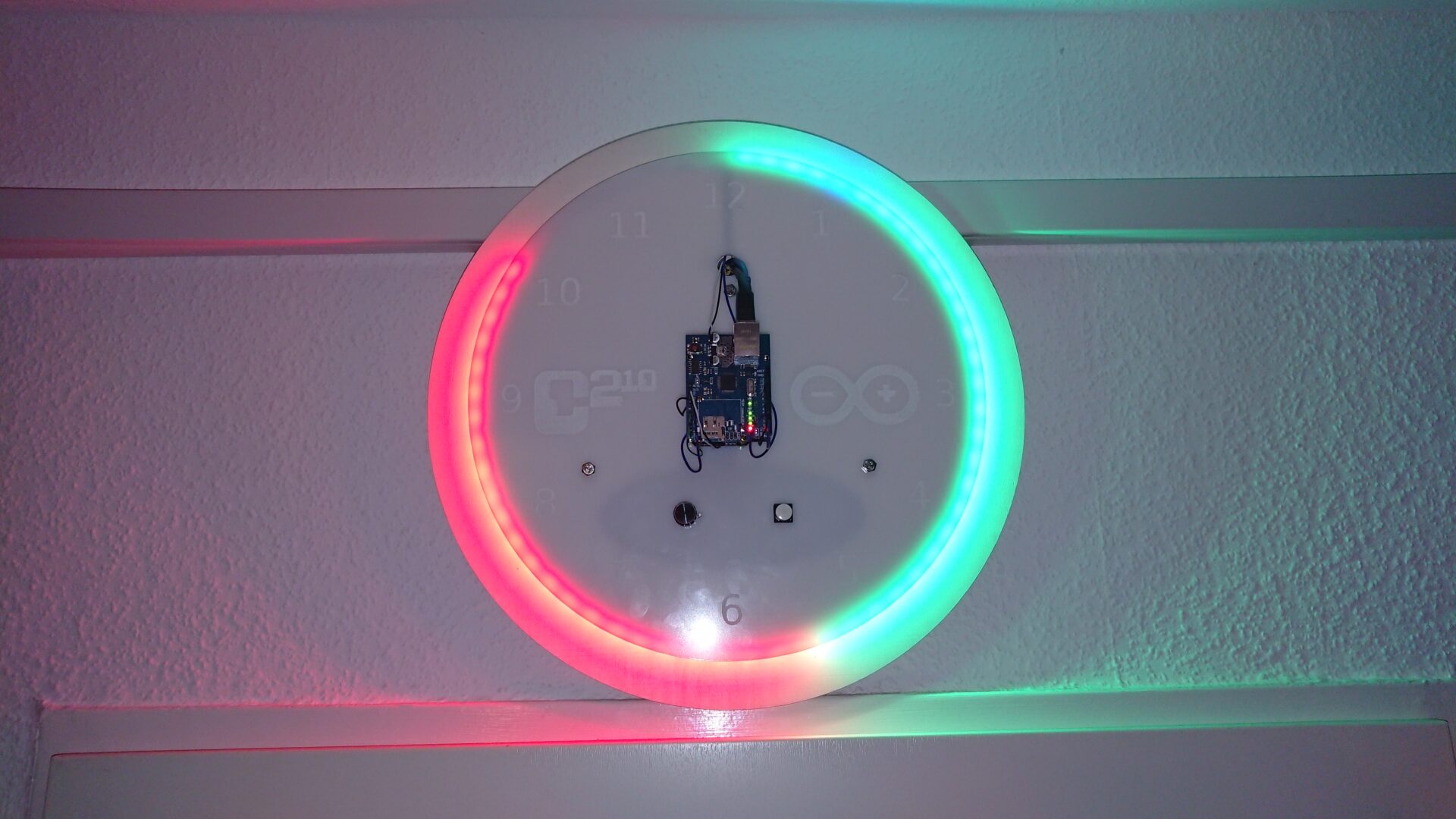
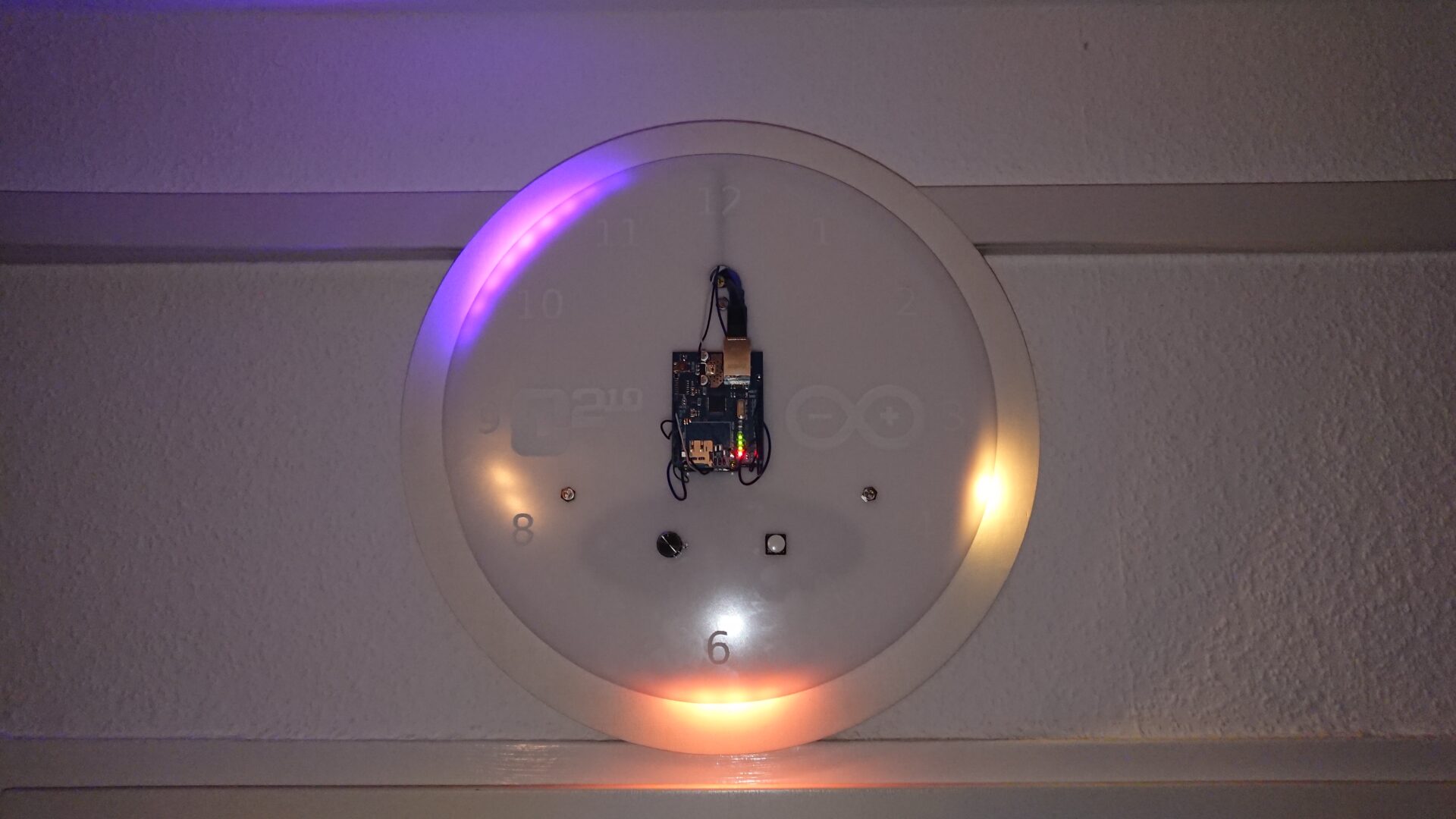
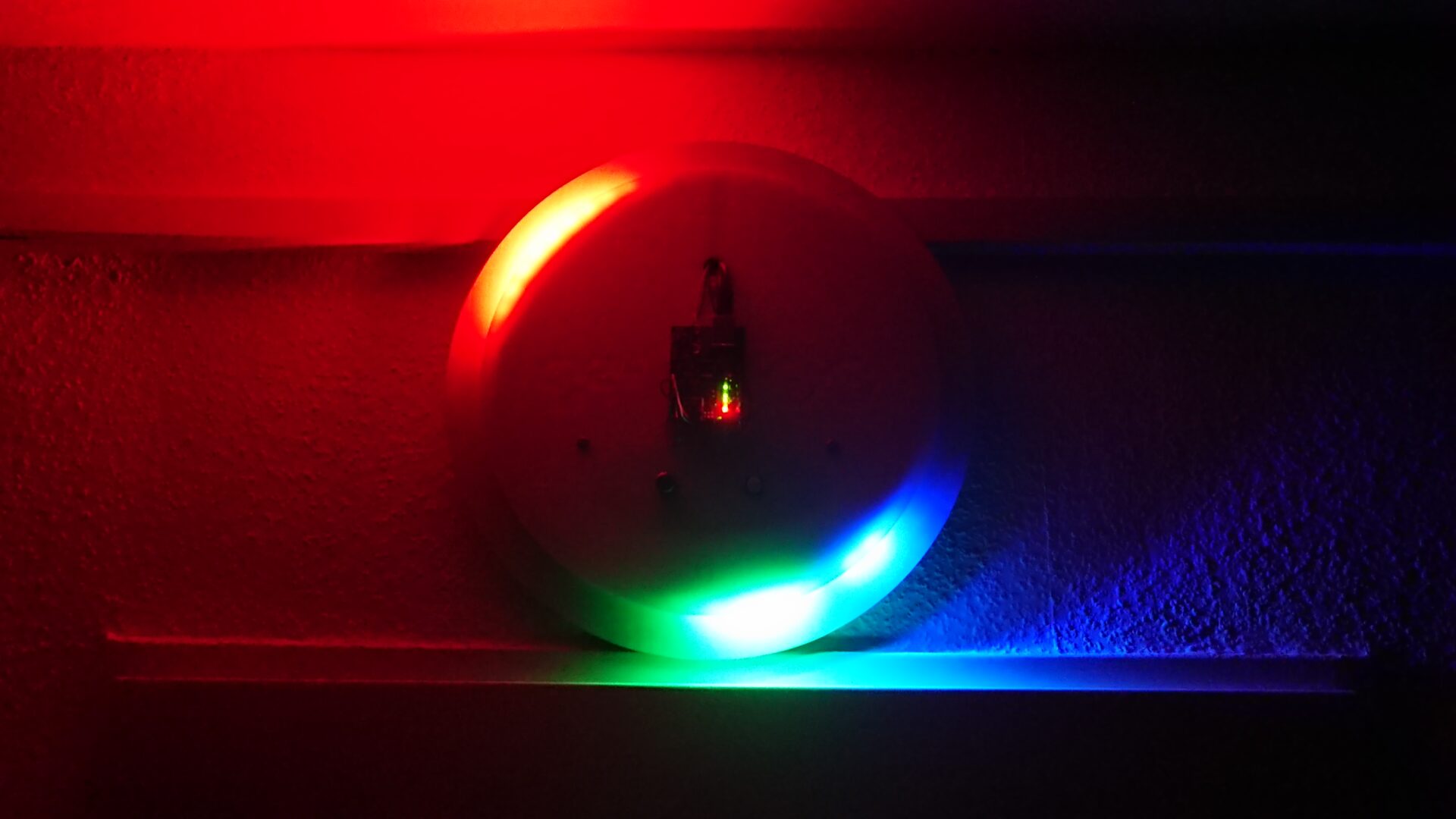
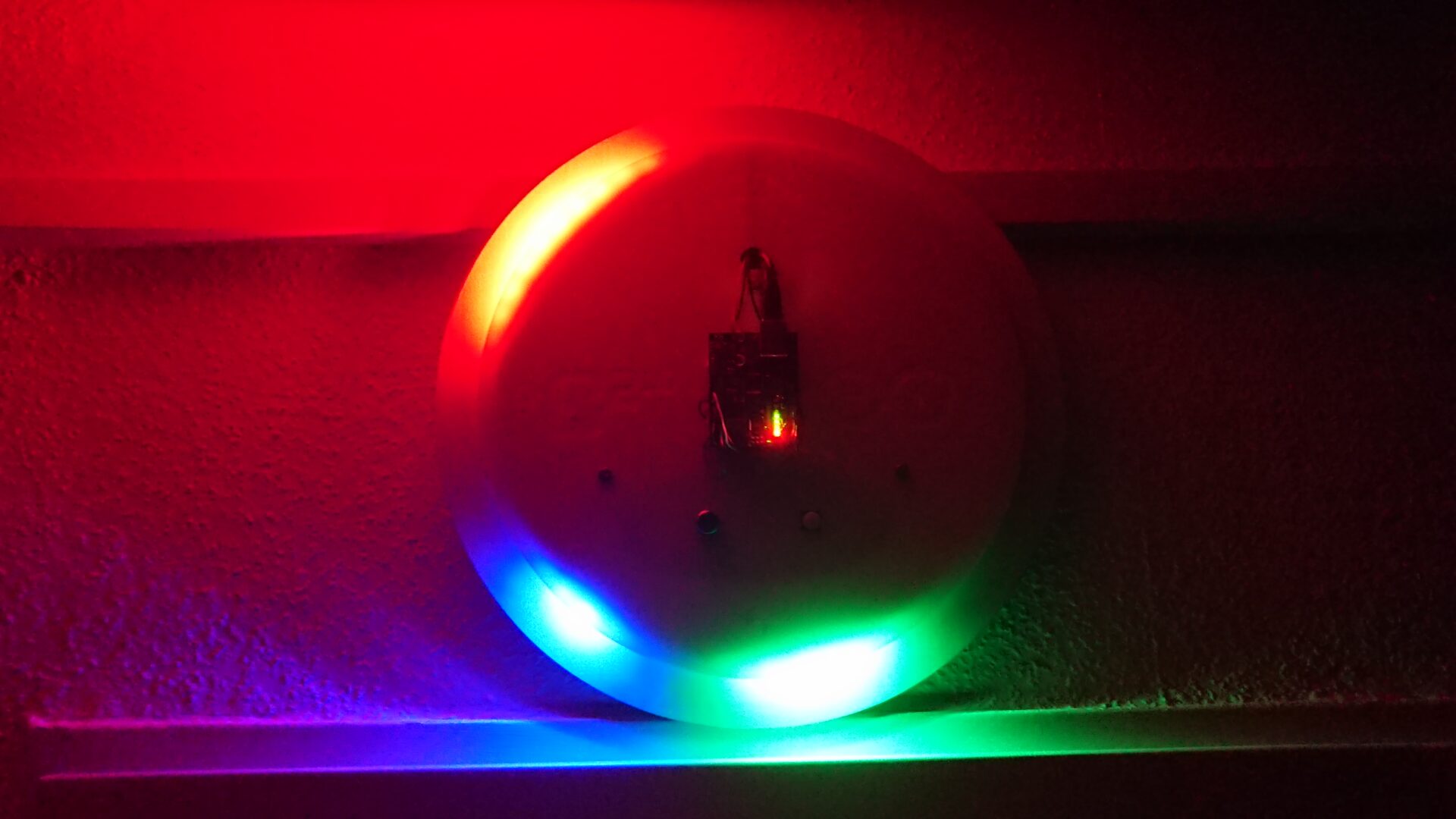
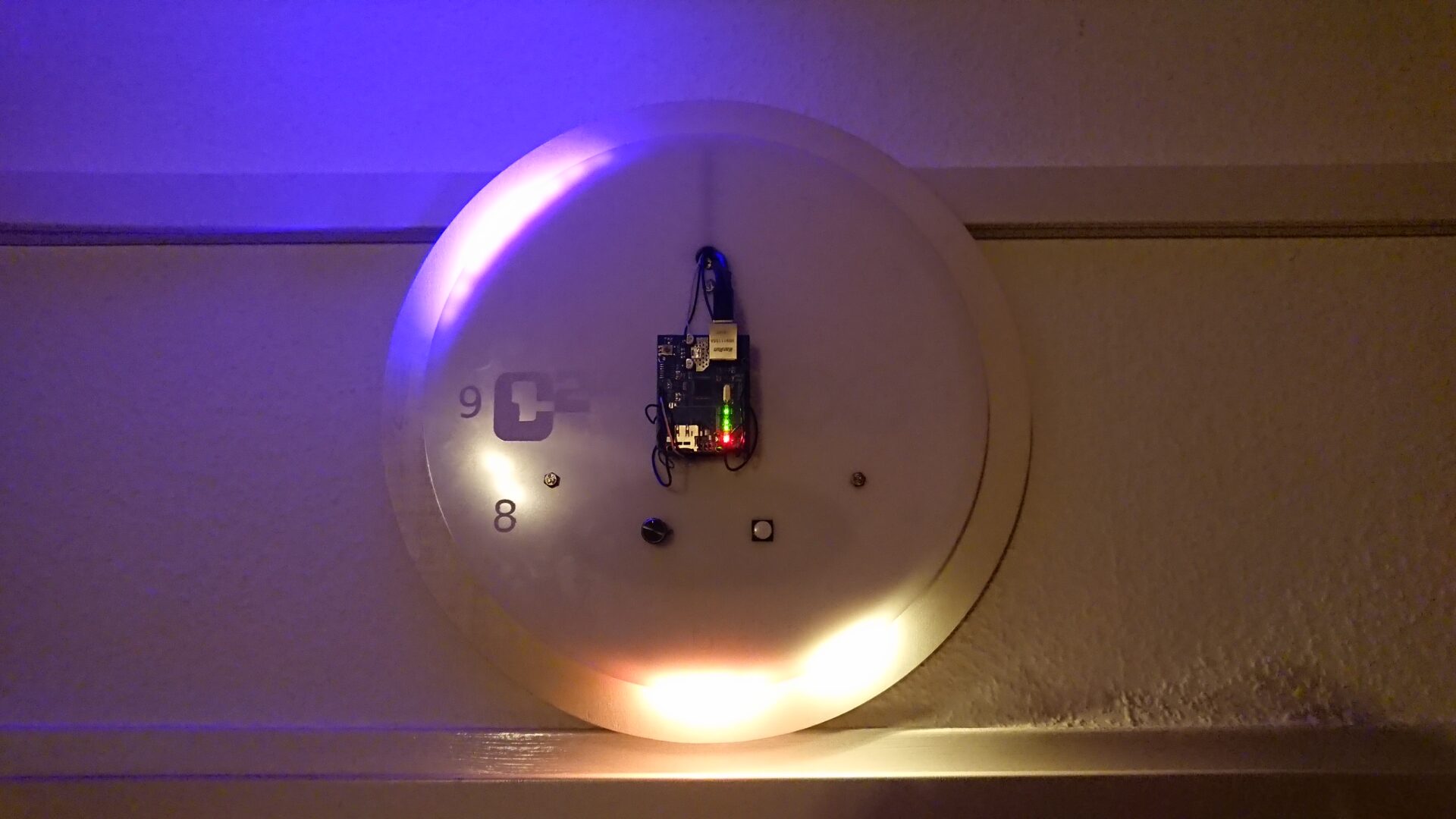
[…] eigentlichen Bau der Uhr dokumentiere ich dann in einem weiteren Artikel, da dieser schon recht lang […]